New plants and facilities
The future of Aluminium:
a sustainable production
VISAC’s
mission

Doing more, with less, is possible. Even in our industry.
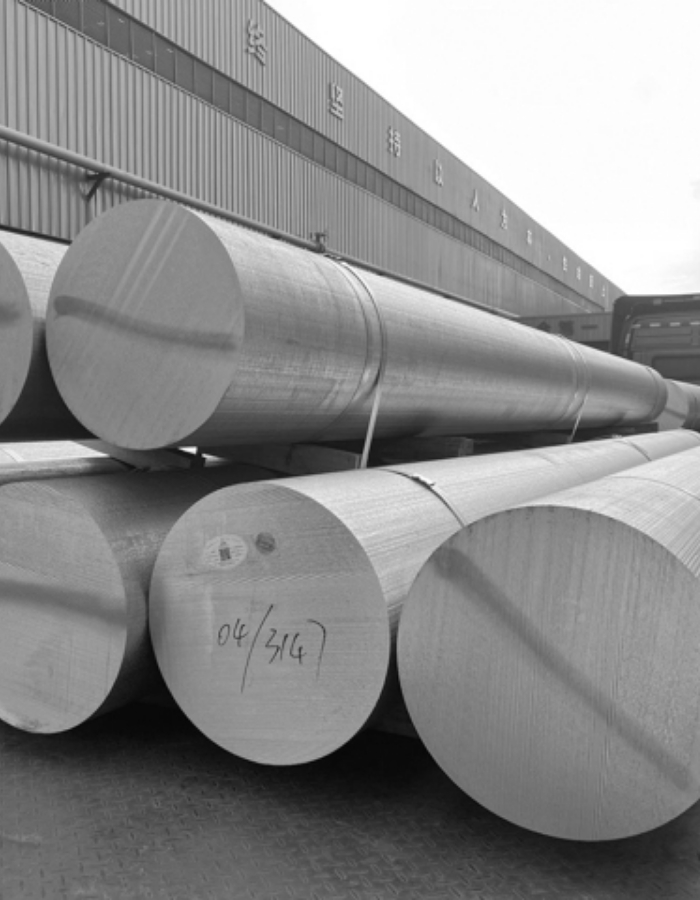
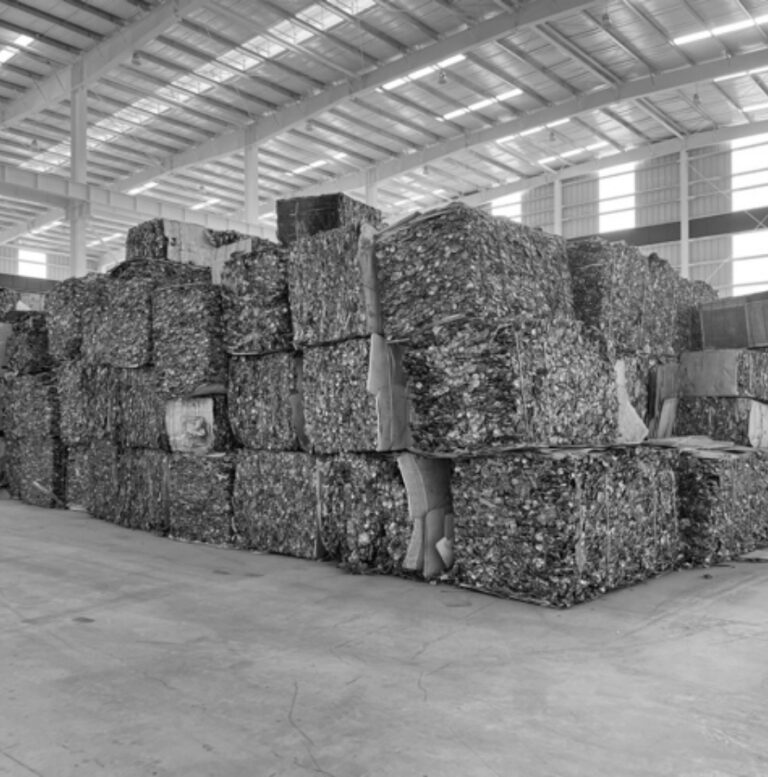
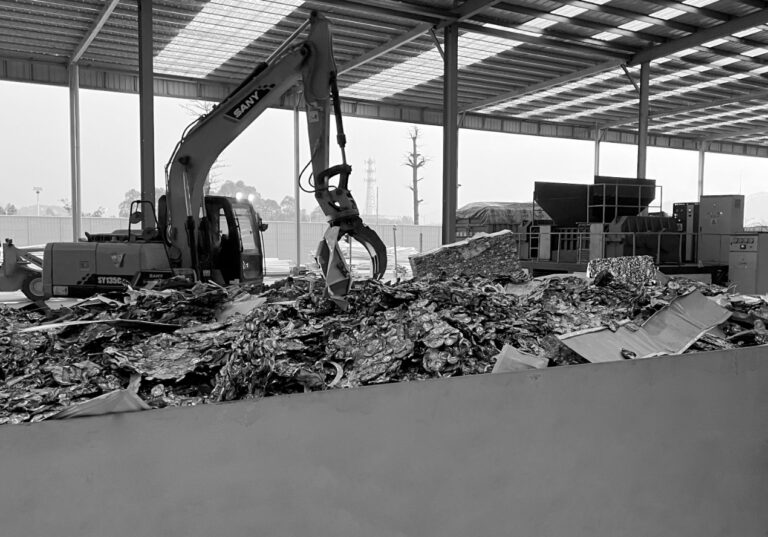
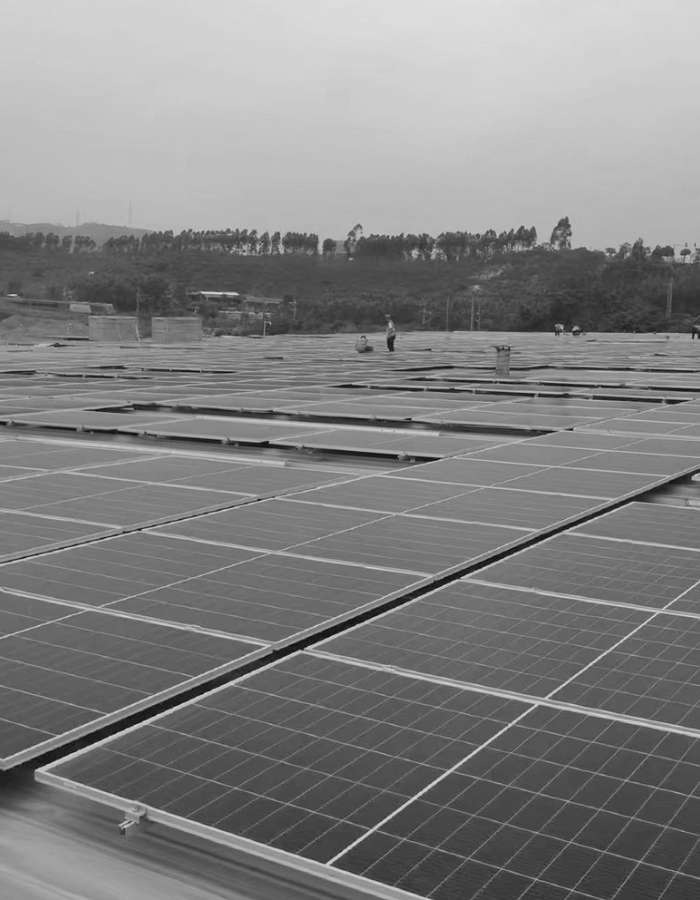
How do we promote
sustainability?
Aiming for sustainable production means investing in resource and energy efficiency, promoting and incentivizing processes and infrastructure with low environmental and social impact.
Aluminium does not age like other organic materials and needs no protection from ultra-violet light. Its overall life-cycle is more environmentally friendly due to the minimum energy required in maintenance and the well-established, proven design life of aluminium assures that it will provide a long term solution year on year with the guarantee of 100% recyclability at the end of a building’s life.
Producing sustainable aluminum means optimizing consumption by renovating plants, acquiring energy resources with a low environmental impact, installing power generation facilities, recycling production waste, organizing and optimizing processes, and reducing pollution and CO2 emissions.
Foundries, presses, surface finishing equipment, and processing machinery must be optimally located within the plants, thus reducing all forms of transportation, while personnel movements over long distances can be done through electrically powered vehicles.
Cutting-edge manufacturers in recent years have devoted considerable resources to the development of sustainable lead-free alloys while maintaining the physical-mechanical properties, such as 2033LF alloy or 6026LF alloy.
Originally, the production of aluminum is through an electrolytic process of extraction from bauxite: this is a highly energy-intensive process with huge CO2 and greenhouse gas emissions into the atmosphere, in which 15 Kw are required to produce 1 kg of aluminum.
Today, the use of processing waste or scrap – thanks in part to new technologies – makes it possible to produce a secondary aluminum quite similar to the primary one, with the advantage of reducing energy consumption by 95 percent and significantly reducing environmental impact.
Through new technologies to improve energy efficiency such as cogeneration, heat recovery and the optimization of manufacturing processes, our reference manufacturers have managed to significantly reduce energy waste.
This reduction, combined with the new photovoltaic systems, places these suppliers among the most advanced and least impactful companies in the world of aluminum producers.
Inside the production cycle, Energy suppliers must be carefully selected and certified as green energy producers with zero environmental impact.
We work with our suppliers and customers to promote the adoption of circular economy practices, which involve the reuse and recycling of materials throughout the entire value chain.
We offer training and awareness programs to our workforce to promote a corporate culture focused on the values of sustainability and inclusiveness.